Predictive Analytics & Maintenance
Manufacturing Predictive Analytics: An Emerging Technology
Rhino Tool House is very engaged in predictive analytics, a pillar of Industry 4.0. Implementations are becoming increasingly common. The goal of industrial predictive analytics is to identify future outcomes based on historical data. Getting from the past to the future relies on data and statistics. The goals of using manufacturing predictive analytics software are to enhance operations, improve quality, and increase efficiency through better inventory forecasting, distribution and resource management.
This is a hot topic as the industrial sector inches towards more connected factories. Most of our customers, especially the major OEMs, have assembled an Industrial Internet of Things (IoT) or Industry 4.0 team to explore practical ways to implement predictive analytics solutions into a factory setting. If they aren’t finding solutions to immediately implement, they are moving processes and capabilities towards implementation. This may be as simple as upgrading “dumb” tools to “smart” tools, installing third-party sensors or networking previously un-networked nodes.
Predictive Maintenance
Predictive Maintenance is used by maintenance teams to reduce unplanned downtime and increase maintenance efficiency, saving money by using machine-learning algorithms to automatically forecast machine failure and remaining useful life. Predictive Maintenance solutions provided by Rhino Assembly achieve a typical ROI of less than 3 months. Driven by Industry 4.0 / the Industrial Internet of Things (IoT), industrial operations are increasingly autonomous. Factories contain numerous sensors that provide real-time data on the status of production and machinery to optimize operations. Welcome to the fourth Industrial Revolution. Unplanned downtime for emergency maintenance is a major pain point and opportunity cost for manufacturers. Current methods for addressing this are largely reactive and not conditions based. Maintenance planning is time-based or use-based, neither of which determines actual need, which leads to excessive or unnecessary inventory of spares and replacements as well as unnecessary maintenance costs (e.g., evaluation of tools that require no maintenance). Instead of performing tool maintenance at a predetermined time interval, what if our assembly tools could tell us when they require service based on a set or series of related conditions?! Industrial predictive maintenance is what customers are looking for, and that is exactly what we can provide.
Getting to Effective Predictive Maintenance Software
Unlike preventive maintenance that assesses conditions in the present, industrial IoT-based predictive maintenance uses real-time monitoring devices such as data sensors on tools and parts to anticipate when replacement is needed, if service is needed and the probability that they will fail during a certain period. While in use currently to a limited extent, scalable technology for this revolutionary solution isn’t readily available, although we imagine that practical manufacturing predictive maintenance applications will likely involve intelligent fastening and/or DC electric torque tools.
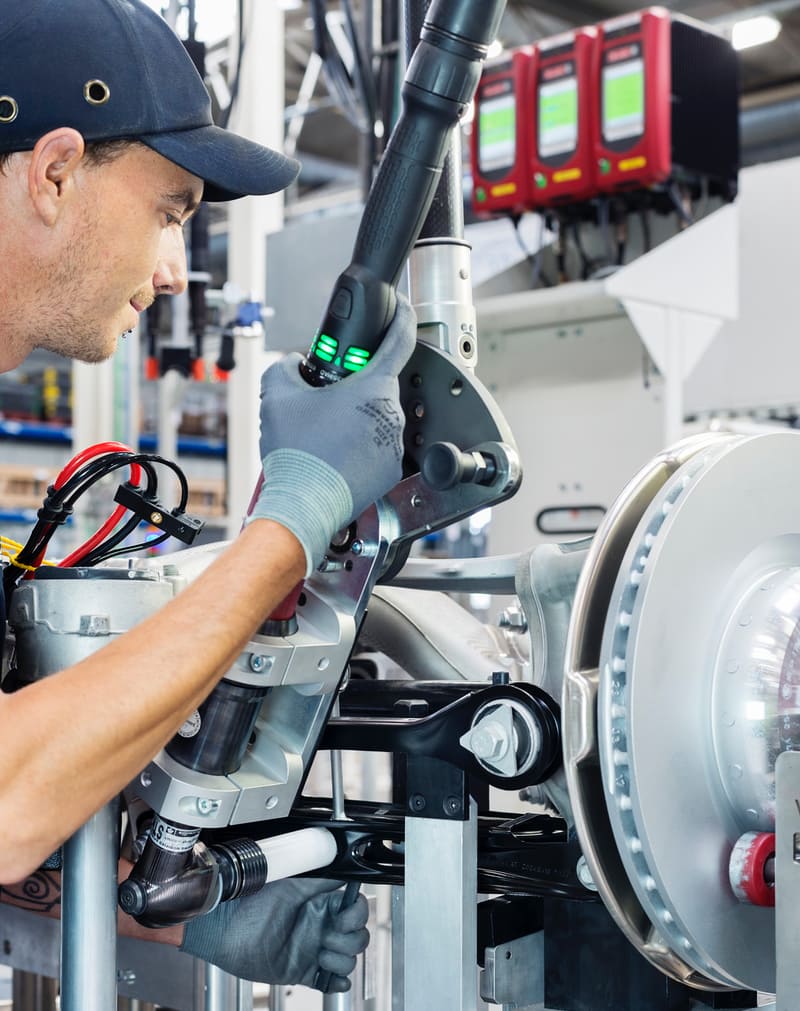
Let Us Walk Your Line & Revolutionize Your Process
We Don't Just Know Products - We Know Applications
What Sets Rhino Tool House Apart for Predictive Analytics & Maintenance?
Rhino Tool House is the leader in cordless assembly solutions. Our highly trained and experienced team is available to visit your facility to help you determine how and where cordless technology is best suited for your specific needs and manufacturing environment. We also help train your team on the use and maintenance of this technology. Start utilizing battery-operated tools today and realize the benefits of improved quality, safety and productivity.